
Ianadmin
Changes in Walki's organization
To realize Walki's strong growth ambitions in the Asia Pacific region, it has been decided that as of January 1, 2012 Mikael Nováky will fully concentrate on growing the business in the Asian markets in his role as Vice President, Asia Pacific. Mikael's responsibilities include all sales and business development activities of the Group in the APAC area and the Changshu plant.
As a consequence, Timo Finnström has been appointed Vice President, Paper Packaging and Sourcing, as of January 1, 2012. Both Timo and Mikael will continue to report to Leif Frilund.
Starting January 1, 2012 the Operational Excellence model will be strengthened by bringing together our Lean and Supply Chain operations into one organization. The Operational Excellence function will concentrate on improving Walki's competitiveness and customer service, and further developing and implementing Lean practices and continuous improvement.
Tuomo Wall, currently Vice President, Sales and Marketing, Technical Products has been appointed Vice President, Operational Excellence as of January 1, 2012. In this new role Tuomo will report to Leif Frilund.
Arno Wolff, currently Vice President, Sales and Marketing, Paper Packaging has been appointed Vice President, Sales and Marketing, Technical Products as of January 1, 2012. Arno will transfer to the new role gradually by April 1, 2012. Arno will report to Wolfgang Thissen, Vice President and General Manager, Technical Products; and concerning Paper Packaging to Timo Finnström.
Nalco 3D TRASAR(R) Technology Helps Freescale Semiconductor Reduce Water Use
Nalco, an Ecolab company (NYSE:ECL), has helped Freescale Semiconductor's Oak Hill fabrication plant in Austin, Texas, respond to severe drought conditions by enabling a substantial reduction in the use of municipal fresh water and increasing water reuse and recycling.
Headquartered in Austin, Freescale Semiconductor is a global leader in the design and manufacture of embedded semiconductors for the automotive, consumer, industrial and networking markets. Freescale's home state of Texas is facing punishing drought conditions, recently recording the state's driest 12-month period on record. The U.S. Department of Agriculture drought monitor shows 80 percent of the state in either extreme or exceptional drought.
Semiconductor manufacturing requires substantial amounts of water, including large chiller systems that regulate temperature and humidity within the manufacturing process to ensure chip quality. Freescale Semiconductor has made a commitment to reduce its manufacturing operations' water consumption by 50 percent by 2015.
To help achieve this commitment, an alternative to municipal fresh water was considered for use in the Oak Hill facility's cooling system — the water used in the manufacturing process to wash the surface of the silicon wafers after polishing. However, contaminants from the wash process could cause numerous problems in the cooling system, including corrosion or microbio fouling and scale buildup that can reduce cooling efficiency.
By implementing Nalco's Green Chemistry award-winning 3D TRASAR® Technology for Cooling Water, Freescale is safely using the reclaimed manufacturing process water. Using fluorescent molecules tagged to water treatment chemicals and a fluorescent bio-reporter molecule, the 3D TRASAR system can continuously monitor and adjust Nalco's patented chemistry to the appropriate level to protect Freescale's cooling system.
In addition, Freescale's Oak Hill site is now using Nalco's PORTA-FEED® Delivery System, which provides "hands-off" chemical handling through a variety of returnable chemical containers. These units replace the need for traditional 55-gallon drums, improving employee safety and reducing the likelihood of spills or leaks and eliminating waste.
Source: Ecolab Inc.
Kemira Oyj: Proposals of the Nomination Board
The Nomination Board proposes to the Annual General Meeting of Kemira Oyj that six members (previously seven) be elected to the Board of Directors and that the present members Elizabeth Armstrong, Winnie Fok, Juha Laaksonen, Kerttu Tuomas and Jukka Viinanen be re-elected as members of the Board of Directors and Jari Paasikivi be elected as a new member of the Board of Directors. The Nomination Board proposes that Jukka Viinanen will be elected as a new Chairman of the Board of Directors and that Jari Paasikivi will be elected as a new Vice Chairman. Currently Pekka Paasikivi is the Chairman of the Board of Directors and Jukka Viinanen is the Vice Chairman.
Mr. Jari Paasikivi (b. 1954). M.Sc. (Econ.) is currently working as President and CEO of Oras Invest Ltd. He is currently also the Chairman of the Board of Tikkurila Oyj and Uponor Oyj and a Board member of Oras Oy.
The Nomination Board proposes to the Annual General Meeting that the remuneration paid to the members of the Board of Directors will remain unchanged. The fees would thus be as follows: the Chairman will receive EUR 74,000 per year, the Vice Chairman EUR 45,000 per year and the other members EUR 36,000 per year. A fee payable for each meeting of the Board and its committees would be for the members residing in Finland EUR 600, the members residing in rest of Europe EUR 1,200 and the members residing outside Europe EUR 2,400. Travel expenses are proposed to be paid according to Kemira's travel policy.
In addition, the Nomination Board proposes to the Annual General Meeting that the annual fee be paid as a combination of the company's shares and cash in such a manner that 40% of the annual fee is paid with the company's shares owned by the company or, if this is not possible, shares purchased from the market, and 60% is paid in cash. The shares will be transferred to the members of the Board of Directors and, if necessary, acquired directly on behalf of the members of the Board of Directors within two weeks from the release of Kemira's interim report January 1 - March 31, 2012. The meeting fees are proposed to be paid in cash.
The Nomination Board has consisted of the following representatives: Jari Paasikivi, President and CEO of Oras Invest Oy as the Chairman of the Nomination Board; Kari Järvinen, Managing Director of Solidium Oy; Risto Murto, Executive Vice-President, Varma Mutual Pension Insurance Company and Timo Ritakallio, Deputy CEO, Ilmarinen Mutual Pension Insurance Company as members of the Nomination Board and Pekka Paasikivi, Chairman of Kemira's Board of Directors as an expert member.
Resolute Extending Offer for Fibrek to February 13
AbitibiBowater Inc., doing business as Resolute Forest Products ("Resolute") (NYSE: ABH) (TSX: ABH), has announced that it extended to February 13 the expiry date for its offer to acquire all the issued and outstanding common shares of Fibrek Inc. (Fibrek, TSX: FBK). The extension is intended to allow the Canadian Competition Bureau to complete its review of the proposed acquisition following its request for supplementary information and the Bureau de révision et décision (Québec) to hear Resolute's application for an order to cease trade the Fibrek shareholder rights plan (the "tactical poison pill").
"A supplementary information request is a normal part of the regulatory process," said Richard Garneau, President and Chief Executive Officer. "We will continue to work with the Canadian competition authority and provide it with the responsive information." He added: "We're pleased to see that over 57% of Fibrek shares have been tendered as of today. The success of our bid should be up to shareholders, unimpeded by management entrenchment maneuvers like the tactical poison pill."
Fibrek shareholders should consider the following factors in making their decision to accept the offer:
- The offer represents a substantial premium to Fibrek's pre-announcement trading price;
- The offer is not subject to any financing condition;
- Fibrek shareholders have the opportunity to exchange their shares of Fibrek, which had been thinly traded through to the date the offer was announced;
- Resolute is uniquely positioned to integrate Fibrek into its existing operations;
- Fibrek shareholders who become Resolute shareholders will own shares in a company that:
- is financially stronger;
- has a diversified asset and product base;
- is determined to continue improving the competitive position of its mills by focusing on cost optimization;
- maintains a prudent capital structure, with a ratio of long-term debt to last twelve months adjusted EBITDA of 1.3x as of the end of the third quarter of 2011.
The offer, which Resolute is making together with RFP Acquisition Inc., a wholly-owned subsidiary, is more fully described in the offer circular and other ancillary documentation the Company filed on December 15, 2011, on the Canadian Securities Administrators' website ("SEDAR"), as amended by notice of variation on January 9 and on January 20. The offer will expire at 5:00 p.m. (Eastern Standard Time) on February 13, 2012, unless it is extended or withdrawn by Resolute. As of the close of market on January 20, approximately 74.25 million common shares of Fibrek had been tendered to the offer, representing approximately 57.1% of the outstanding common shares.
The offer is subject to certain conditions including, among others, a 66⅔% minimum tender condition, waiver or termination of all rights under the shareholder rights plan, receipt of all regulatory, governmental and third-party approvals, consents and waivers, Fibrek not having implemented or approved any issuance of shares or other securities or any other transaction, acquisition, disposition, capital expenditure or distribution to its shareholders outside the ordinary course of business, and the absence of occurrence or existence of any material adverse effect or material adverse change. Subject to applicable laws, Resolute reserves the right to withdraw or extend the offer and to not take up and pay for any Fibrek common shares deposited under the offer unless each of the conditions of the offer is satisfied or waived (at its sole discretion). The offer is not subject to any financing condition.
Questions and requests for assistance or further information on how to tender Fibrek common shares to the offer should be directed to, and copies of the above referenced documents may be obtained by contacting, Georgeson at 1-866-598-0048 or by email at This email address is being protected from spambots. You need JavaScript enabled to view it.
Source: Resolute Forest Products
James C. Tyrone Returns to NewPage
NewPage announced today that James C. Tyrone has accepted the role of executive vice president, Commercial Operations and Business Development, effective February 1, 2012. Mr. Tyrone will report to George F. Martin, president and chief executive officer.
Effective with Mr. Tyrone's return, the Sales and Marketing, Order Management and Strategy groups will be realigned under his direction. Barry Nelson, senior vice president, Sales and Marketing will report directly to Tyrone and retain his current roles and responsibilities, as will Linda McClinchy, vice president, Order Management and Curtis Short, vice president, Strategy.
Mr. Tyrone was most recently with Appleton Papers, where since 2010 he served as senior vice president responsible for Appleton's thermal paper business unit and oversight of the company's paper manufacturing operations. He started his paper industry career with The Mead Corporation in 1990, serving in a variety of roles. When Mead and Westvaco merged, Mr. Tyrone was senior vice president of Sales and Marketing, a role he continued when NewPage started in May 2005. Before Mead, he worked for seven years as a senior manager for McKinsey & Company.
Mr. Tyrone has a bachelor's degree in chemical engineering from the University of Virginia, and a master's degree in business administration from Harvard University.
Mercer International Inc. Announces Expansion Project at Its Stendal Mill
Mercer International Inc. has announced a project ("Project Blue Mill") to increase production and efficiency through debottlenecking initiatives including the installation of an additional 40 MW steam turbine at its Stendal mill. The debottlenecking which, among other things, requires the new turbine in order to enhance and efficiently utilize steam production, is designed to increase the mill's annual pulp production capacity by 30,000 ADMTs to approximately 675,000 ADMTs. The new turbine is also expected to initially produce an additional 109,000 MWh of surplus renewable energy for sale at premium pricing.
"We are very pleased with this project," said Jimmy Lee, President and CEO. "The project allows us to maximize the value from the wood that we process at Stendal, increase production and efficiency, provide a backup generator on the first turbine and reduce energy costs during maintenance periods and expand power generation. We currently expect the project, in addition to enhancing mill operating results, to deliver approximately €7.5 million (U.S. $9.8 million) of additional annual power revenues."
Mr. Lee concluded: "The project is in line with our group's overall focus on enhancing revenues from the production of green energy and other by-products at all of our mills. We believe that our generation and sale of surplus renewable energy and by-products give Mercer a competitive energy advantage over less efficient mills and provides us with a stable revenue source unrelated to pulp pricing. Based upon our overall 2011 production and sales, after giving effect to Project Blue Mill, on a consolidated basis, we currently expect Mercer will produce about 760,000 MWh of annual surplus renewable green energy and generate approximately €65.5 million (U.S. $84.5 million) of associated revenues therefrom. Since our energy production is a by-product of our pulp production process there are minimal incremental costs and our surplus energy sales are highly profitable."
Project Blue Mill will require approximately €40.0 million in capital expenditures over about 21 months. The project is eligible for €12.0 million of non-refundable German government grants and the Stendal mill has secured a new €17.0 million five year amortizing secured term debt facility, of which 80% will be government guaranteed. The facility is non-recourse to Mercer. The balance of the project will be funded through operating cash flow of the Stendal mill and up to an aggregate of €8.0 million in pro-rata shareholder loans from Mercer and its minority partner. Project Blue Mill is currently designed to be completed and start to generate power revenues in or about September, 2013.
The Stendal mill is a state-of-the-art, single-line NBSK pulp mill situated near the town of Stendal, Germany with a current annual pulp production capacity of approximately 645,000 ADMTs.
ABB Wins Upgrade Order to Improve Paper Quality at U.K. Mill
New systems will help diversify products at DS Smith Paper’s Kemsley Mill
ABB, the leading power and automation technology group, recently won an extensive order to upgrade automation at DS Smith Paper Ltd’s Kemsley Mill in Sittingbourne, Kent, England. The new systems will help the mill produce a greater diversity of high quality paper products.
The order includes an upgrade of the mill’s PM3 automation and drives systems, including a new Quality Control System (QCS), upgraded and expanded Distributed Control System (DCS) and upgraded and expanded Drive System, as well as a new Web Imaging Solution (WIS). All of the systems will be integrated with the existing System 800xA.
The mill’s Advant QCS will be upgraded to an 800xA with two new Network Platforms and an Air Water Spray. The drives upgrade includes new ACS800 drives and AC800M Controllers. One of the existing DCS Advant Controllers will be upgraded to an AC800M and integrated into the system.
The new QCS will help improve product quality on the PM3, while it increases production and reduces costs. ABB’s System 800xA DCS will provide a solid platform for the mill’s integrated process operation. The upgraded ABB drives will deliver fast start ups and benefits over the equipment lifecycle that include increased productivity, improved quality and energy savings, while the new WIS will give the mill a state-of-the-art tool for identifying web defects and managing visual uniformity.
The Kemsley Mill is rebuilding its PM3 so it can produce highest quality linerboard and white-top liner grades.
The new systems will be ready for start-up in June 2012.
Source: ABB
M-real renews its management and reporting structure
M-real operates through two business areas that are also the company’s reporting segments from first quarter of 2012 onwards:
- Paperboard
- Paper and Pulp
Pasi Piiparinen (50) has been appointed SVP, Head of Paperboard business area and a member of M-real Corporate Management Team as of 20 March 2012. Piiparinen reports to CEO Mikko Helander. Piiparinen joins M-real from Stora Enso where his latest position was SVP, Sales and Marketing, Fine Paper Business Area. Piiparinen has an extensive background also in Stora Enso’s packaging business. His education is Master of Science, Engineering.
As earlier announced, Mika Joukio, current SVP, Head of Paperboard business area has been appointed CEO of Metsä Tissue Corporation as of 1 February 2012. After Mika Joukio leaves and before Pasi Piiparinen starts in his new position, CEO Mikko Helander will be the acting Head of Paperboard business area.
M-real's Corporate Management Team consists of the following persons:
- Mikko Helander, CEO, also acting Head of Paperboard business area starting from 1 February 2012 until 19 March 2012
- Matti Mörsky, CFO
- Pasi Piiparinen, SVP, Head of Paperboard business area as of 20 March 2012
- Seppo Puotinen, SVP, Head of Paper and Pulp business area
- Sari Pajari, SVP, Supply Chain and Business Development
- Mika Paljakka, SVP, HR
- Jani Suomalainen, SVP, Procurement
The changes in management structure take effect immediately.
Soili Hietanen and Heikki Husso will step out of M-real’s Corporate Management Team. Husso continues as the Managing Director of M-real Zanders GmbH while Hietanen will work in different development projects in the M-real head office.
Paperboard business area includes the Kemi, Kyro, Simpele, Tako and Äänekoski board mills, Kyro wallpaper base machine and Joutseno BCTMP mill located in Finland as well as Gohrsmühle mill in Germany. Paper and Pulp business area includes Husum paper and pulp mill in Sweden, Alizay mill in France and Kaskinen BCTMP mill in Finland.
As earlier announced, M-real is planning to close the entire Alizay mill and the unprofitable operations at Gohrsmühle mill. The plans are expected to materialize in early 2012 that would improve the company’s profitability materially.
The accounting treatment of the M-real’s 32 percent ownership in Metsä-Botnia will remain unchanged. The associated company result of Metsä-Botnia will be allocated to business segments based on their respective pulp consumption. Roughly two thirds of the result impact of Metsä-Botnia ownership is expected to be included in the Paperboard business area and the rest in Paper and Pulp business area.
M-real will announce its financial statements 2011 on 9 February 2012 based on the old business area and reporting structure. The restated historical figures based on the new business structure will be released during the second half of February 2012.
Paper & Plastics Recycling Conference - Middle East
The event, scheduled for 27 – 28 February in Dubai, UAE, is designed for private recyclers, public waste management officials, private waste management firms, merchants and brokers, equipment suppliers and consumers of these materials.
Why Attend?
· Learn about recycling and waste management development plans from the perspective of leading public officials.
· Get in-depth insight into the commodity markets for recovered paper and plastic and the demand trends that will affect those markets.
· Discuss quality challenges inherent in collecting more fibre in co-mingled methods.
· Learn about state-of-the-art processing equipment and technology.
· Benefit from networking opportunities that can enhance your trading opportunities.
To view the complete schedule of events, click here
To register, click here
Click here to learn more or contact This email address is being protected from spambots. You need JavaScript enabled to view it. to receive updates on the event.
Mondi launches promotional campaign
Mondi highlights key benefits of ColorLok® Technology with a new campaign and a chance to win a trip to the Sahara, Barcelona or Norway to see the polar lights.
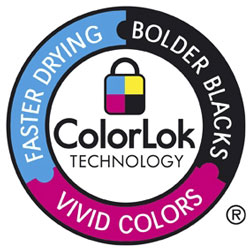
For a chance to win one of these prizes, customers must enter a ColorLok® code at www.mondigroup.com/colorlok. Codes can be found on promotional stickering on A4, 80 g/m2 reams of Mondi papers with ColorLok® Technology as well as scratch-and-win lottery tickets distributed in magazines and by sales agents. Further codes will also be issued per valid email address entered on www.mondigroup.com/colorlok. See full contest details and regulations at the Mondi ColorLok® website.
Recently, Mondi added BIO TOP 3® extra, 100% recycled NAUTILUS® SuperWhite, IQ appeal and MAESTRO® bulky to its ColorLok® paper portfolio, which also includes IQ premium, IQ selection smooth, MAESTRO® extra, MAESTRO® supreme, DNS® premium, and NAUTILUS® ReFresh TRIOTEC. According to Johannes Klumpp, Marketing and Sales Director for Mondi Uncoated Fine Paper Sales, ColorLok® Technology is an added value for customers who use inkjet printers.
“In smaller office and home environments, where most inkjet printing takes place, our papers treated with ColorLok® Technology deliver richer, more vibrant image reproduction, sharp text and reduced ink smears because of the faster drying time. Our customers can see the difference between inkjet printing on paper with and without ColorLok® Technology,” says Johannes Klumpp.
ColorLok® Technology is based on a class of paper additives that visibly enhance the print quality of inkjet documents while also providing faster drying time. A specific chemical interaction between additives and the pigment holds the pigment on the paper surface while the rest of the ink penetrates deep into the paper, resulting in the crisp, vivid print quality.
Mondi ColorLok® campaign on www.mondigroup.com/colorlok will run from January-June, 2012.