Custom corrugated boxes and fiber tubes protect products and the environment and build brand image
By Cheryl Smith
The subject of packaging and shipping solutions has become an increasingly popular topic of conversation within businesses and among the public.
Before and during the pandemic, the rapid expansion of e-commerce has fueled demand for packaging, while labor shortages and shipping constraints have also made it harder to produce and deliver the containers used to ship and store everything from food and consumer goods to machine parts.
At the same time, consumers are increasingly aware of the need for more sustainable packaging. According to McKinsey & Company, 55% of US consumers are extremely or very concerned about the environmental impact of packaging. They are willing to pay more for eco-friendly products, and they express a desire to buy additional sustainably packaged products if more of them were available and better labeled to indicate green packaging.
As a result, businesses have responded in three important ways.
First, they have turned to suppliers that have a proven track record and ongoing capability of delivering packaging solutions when needed to ensure that the right shipping container is available when product comes off the production line.
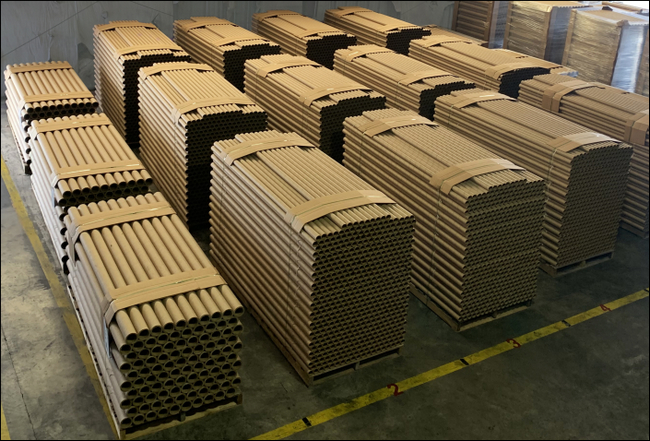
Environmental Sustainability
Second, the demand for corrugated cardboard boxes and fiber tubes expands as consumers, government regulators, investors and employees push for environmentally friendly alternatives to plastics. Boxes and tubes are made from plant-based materials which can be sustainably harvested and replanted, and many boxes and tubes are manufactured from 100% recycled material.
The disposal of these paper-based packaging solutions is also far more sustainable. In 2021, 91.4% of corrugated cardboard was recycled compared to only 6% of the 40 million tons of plastic waste generated in the US. Moreover, the paper is biodegradable and does not contain any toxic chemicals or heavy metals, and therefore the small percentage of scrap or used boxes and tubes that do end up in a landfill will decompose without harming the environment. In fact, boxes and tubes buried in the earth will compost in a couple months, adding nutrients back into the soil.
Custom Packaging Solutions
The third reason for the increased interest in custom boxes and fiber tubes is their versatility and adaptability to perfectly fit the specific requirements of each application to achieve the optimal balance between the crush strength and weight/thickness to reduce the cost of materials and shipping.
Custom packaging comes in many shapes, sizes, and strengths to contain and protect products for storage or transport. The packaging should be designed to fit the product, rather than the other way around.
A perfect fit means eliminating the waste, reducing environmental impact and costs of producing, handling, and disposing of excess packaging and unnecessary void fill material — and of damaged product. The right fit also means higher packing density for more energy-efficient transport and more space-efficient storage.
Custom boxes and fiber tubes also enable important marketing advantages over stock packaging. Graphics and information can be printed on the interior and exterior surfaces to increase brand awareness and support point-of-purchase campaigns.
The two major categories of custom, sustainable packaging are corrugated boxes and fiber tubes. Both categories have the environmental benefits of fiber material, and both are extremely customizable to meet specific application requirements.
Custom Corrugated Boxes
Custom corrugated boxes can be designed in any desired size and in a wide range of board thickness. Designers utilize software to optimize the shape and size of the box to efficiently and safely package the product(s) contained within, and to ensure the boxes can be stacked securely on a pallet, without wasted space.
Boxes hold items wrapped with protective packaging or surrounded with void fill material for safe shipment. They can be sealed, closed, and stacked in a warehouse or shipping container. Some specialty boxes ship hazardous materials or insulate products from excessive heat or cold.
Box types include Die Cut, Full Overlap Slotted Container (FOL), Full Telescopic Design Container (FTD) and Overlap Slotted Container (OSC). A variety of wax and varnish coating options are available. Additional customizations include partitions, eyelets, transparent windows, and die cut foam inserts
Fiber Tubes
Fiber wound tubes are also customized depending upon the specifications and requirements of each customer and applications. They are typically made of cardboard, but they can also be reinforced with other materials for added strength and resilience. Paper or paperboard sheet layers are wound together and bonded with an adhesive to form strong, hollow, and usually cylindrical shapes. Fiber wound tubes provide an excellent strength-to-weight ratio and are used in applications requiring high bend strength, crush resistance, and dynamic strength.
Tubes are available in various sizes; length, inside diameter, and wall thickness can be customized to fit specific products. The wall thickness of the tube can vary depending on the number of layers wrapped during manufacturing. The innermost layer or ply - the liner -, and the outermost layer - the wrap -, can consist of different materials (foil, film, etc.) or specialized paper. The specialized paper and materials can provide water resistance, graphics or labeling, or a specific color.
Tubes Serve as Containers and as Paper Cores
The high strength of fiber tubes makes them well-suited to two very different uses — as an exterior container for a very wide range of products or as the interior core around which sheets of material are wound.
As a container, tubes protect a wide variety of products during shipment, protecting them from damage, including long, heavy items such as pipes and baseball bats, and fragile items such as fishing poles. Tubes are often a good alternative to shipping items in a box with protective packaging or void fill. The range of applications is quite extensive, from small tubes with film barriers for potato chips to large tubes used to form concrete pilings.
Paper cores typically fall into two subcategories: In industrial applications, webs or sheets of flexible material (plastic film, paper, foil, textiles, etc.) are wound around paper cores with thick walls. These tubes function as a machine element and facilitate loading of the large rolls. The other subcategory is a thinner-walled variety of tube used for the packaging and dispensing of retail products, such as the core of aluminum foil, plastic wrap, paper towel and toilet paper rolls, as well as adhesive tape and labels.
Protect Products and the Environment
Custom boxes and tubes are more effective at protecting products than stock boxes, and they have far less impact on the environment compared to plastic packaging. A custom packaging solution means a perfect fit for your product, with less waste and more efficient packing and transport, resulting in cost savings, as well as a distinctive image that enhances brand image and supports marketing campaigns.