The global interest of papermakers in water-saving solutions has steadily increased, with the effective use of water as a resource is an essential lever for sustainable paper production. To support papermakers in securing their future competitiveness, Voith and its subsidiary Meri have been developing tailored new innovations in the areas of water, sludge and residual materials for more than 25 years. Mutual understanding of the product portfolio, very close coordination in every project phase and many successfully completed projects characterize the partnership of the companies. As Axel Gommel, Global Product Manager Fiber Systems at Voith Paper, explains: "Over the years, we have developed unique process know-how. Combined with our highly efficient technologies, this makes Voith a strong full-line partner for manufacturers of all paper grades who want to take their operations to the next level of performance in the area of sustainability."
In successful cooperation, Voith and Meri experts offer fresh water treatment and conditioning as well as internal cleaning of process water streams. In addition to process and disposal machines, their extended portfolio also consist of wastewater treatment including primary, secondary and tertiary treatment via chemical or physical stages. These are combined with anaerobic and aerobic biological processes and sludge treatment. Customers also benefit significantly from Voith and Meri's water and wastewater balances. Furthermore, Meri offers optimized solutions for the rejects recovery process stages, such as transport, handling and conditioning, and waste-to-energy processes.
In addition to the optimized product portfolio and close cooperation, global presence is also a key success factor, as Henning Laubrock, Head of Sales & Technology at Meri, adds: "Thanks to the combined synergies of Voith and Meri, we are very well positioned and networked internationally." Voith now boasts more than 110 OCC stock preparations with a total production capacity of more than 40 million tons per year over the past 20 years. Meri has realized more than 5,000 installations and supplied more than 300 subsystems. With the opening of another site in Kunshan, China, Meri strengthened its local footprint in the APAC region, supplying efficient water, sludge and reject (WSR) and wastewater systems to Chinese and other Asian customers, among others.
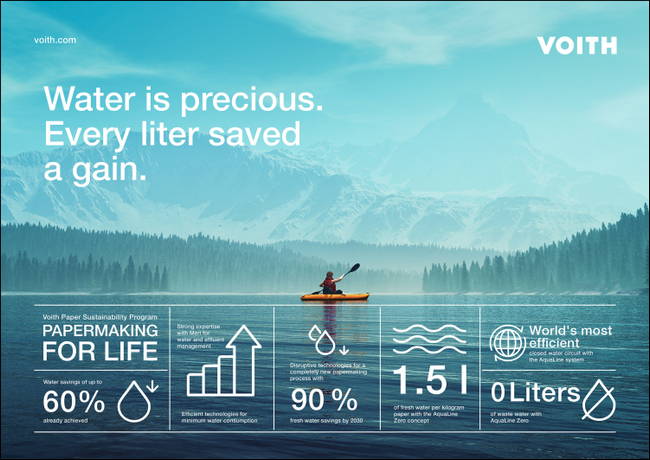
According to Laubrock, a major milestone of Voith and Meri was the joint development of the sustainable water management system AquaLine. Following the official launch of the system in 2021, the AquaLine, AquaLine Flex and AquaLine Zero system variants are already in use at several well-known manufacturers of packaging paper. Among others, the North American paper manufacturer Green Bay Packaging uses the AquaLine Flex system variant at its PM 4 in Wisconsin. Equipped with a "biological kidney," the process water can be treated and part of the purified process water fed back into the production process. The amount of wastewater is thus reduced to up to 3.5 liters per kg of paper produced. Compared to similar production plants, Green Bay Packaging with an annual production volume of 621,422 tons and a design speed of 1,200 m/min saves fresh water amounting to 2,271 m³ per day. Comparable process values and savings can also be found in the plant of Turkish paper manufacturer Kipaş Kağıt, which started up in mid-2022. In addition, Kipaş Kağıt produces around 90 MW of electrical energy from biogas produced in Meri's anaerobic wastewater treatment plant and fed directly into the public grid.
Axel Gommel sums up: "The AquaLine Flex system variant has now become state of the art in the production of packaging papers. In addition, under certain conditions it is possible to operate plants with the closed, technologically very complex water circulation system AquaLine Zero, in which the process wastewater is reduced to zero liters." In the future, Voith will continue to develop the individual concept variants so that closed water circuits can increasingly be used throughout the paper industry. In addition, as part of Voith’s Papermaking for Life sustainability program, the company is also working on new, disruptive solutions to significantly reduce fresh water consumption.
Papermaking for Life sustainability program
Resource efficiency is a key focus of the Papermaking for Life sustainability program. As part of its innovation and development offensive, Voith Paper is presenting versatile technologies and initiatives that lead to more efficient and sustainable processes in paper production. The focus is on water, energy and fiber savings as well as digitalization, innovations and partnerships as levers for more sustainable production. Learn more about the focus topic water here: www.voith.com/papermaking-for-life/water.
About Meri
The MERI Group, a wholly owned subsidiary of Voith Paper, is a global environmental technology company specializing in industrial applications, particularly for the paper industry and food & beverage. Due to the global market trend towards "online shopping", the market of Meri's customers in the recovered paper/recycled based packaging paper industry will continue to grow in the coming years. MERI Group has been a leader in the relevant environmental technology field for the paper industry for years. With offices in Germany, USA, China and Brazil Meri realizes in the application fields: Residual and Fuel Processing, Material Handling, Reject and Sludge Dewatering, Water Treatment, Recirculating Water Purification and Wastewater Treatment single machine projects, upgrades and new construction of complete plants. With over 5000 units installed, Meri has been a reliable partner for customers in the global paper industry for many years, as well as for the market-leading parent company Voith Paper. Tel: +49 89 59 33 44 | Email: This email address is being protected from spambots. You need JavaScript enabled to view it. | https://www.meri.de/
About the Voith Group
The Voith Group is a global technology company. With its broad portfolio of systems, products, services and digital applications, Voith sets standards in the markets of energy, paper, raw materials and transport & automotive. Founded in 1867, the company today has around 21,000 employees, sales of € 4.9 billion and locations in over 60 countries worldwide and is thus one of the larger family-owned companies in Europe.
The Group Division Voith Paper is part of the Voith Group. As the full-line supplier to the paper industry, it provides the largest range of technologies, services and products on the market and offers paper manufacturers holistic solutions from one source. The company’s continuous stream of innovations facilitates resource-conserving production and helps customers minimize their carbon footprint. With its leading automation products and digitalization solutions from the Papermaking 4.0 portfolio, Voith offers its customers state-of-the-art digital technologies to improve plant availability and efficiency for all sections of the production process.